
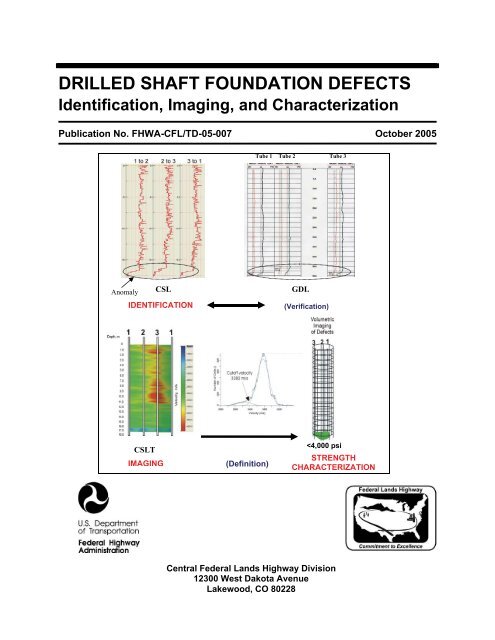
The scenarios included hydraulic jack locations at several distances above and below a caliche layer. Using the calibrated model, several scenarios of hydraulic jack location were simulated.
Drilled shaft plaxis 2d software#
Additionally, the Osterberg test data was used to calibrate a numerical model by Plaxis finite element software for drilled shaft analysis. The hydraulic jack was placed at the midpoint of the drilled shaft length.

In this study, drilled shaft capacities were derived utilizing data from 30 Osterberg full-scale field load tests in soils containing caliche layers. The location of the hydraulic jack with respect to caliche layers influences the measurements obtained from the Osterberg test and the subsequent interpretation of drilled shaft capacity. This study investigates the effect of the location of an O-cell hydraulic jack along the length of a drilled shaft in a full-scale Osterberg test performed in soils containing layers of caliche. The results indicate that displacements under static loading in saturated drained conditions and when non-linear materials are present are the closest to field measured deflections. The materials’ behavior was simulated with nonlinear models: Mohr–Coulomb (MC) for pavement layers and soft-soil model (SSM) for the expansive subgrade, in saturated drained and undrained conditions.

In the new model, the calculation of the transferred pressure to the pavement through contact area of tires is 3D it was turned into a 2D problem, and the pavement was subjected to a static loading using a ratio factor of dynamic additional charge. The numerical analysis is carried out with the Finite Element software package PLAXIS version 2012. As the preliminary step, the deflection measurements were taken at the asphalt surface layer, using a Total station at different distances as function of truckload applications. The existing pavement was replaced and designed based on California Bearing Ratio (CBR) method, with a new one, and subjected to the traffic from various number of load cycles from 12.1 up to 155.52 kcycles of standard axle load (80 kN) through dual wheel assembly over a 6-month period. To study and predict the behavior of flexible pavement over expansive soils, a pavement structure was subjected to different laboratory and fieldwork experiments.
